近年、労働現場における挟まれ事故や巻き込まれ事故は、重大な労働災害の一つとして注目されており、その発生率も無視できません。厚生労働省のデータによれば、令和5年に労働事故で死傷した人のうち、挟まれ事故や巻き込まれ事故は約21%を占めており、安全対策がいかに重要であるかを物語っています。本コラムでは、これらの事故の現状と原因、そして具体的な防止対策について詳しく解説します。
挟まれ事故と巻き込まれ事故の現状
労働現場における安全性は、企業や労働者にとって非常に重要な課題です。特に、挟まれ事故や巻き込まれ事故は重大な労働災害の一つであり、その発生率は無視できません。厚生労働省が公開しているデータによると、令和5年に労働事故で死傷した人のうち、挟まれ事故や巻き込まれ事故は約21%を占めています。このデータは、挟まれ事故や巻き込まれ事故が労働現場で重大なリスクであることを強く示しています。これらの事故は発生すると、深刻な怪我や命に関わる事態を招く可能性が高く、労働者の安全確保において特に注意すべきポイントです。
具体的な事例としては、工場での機械操作中に手や腕が機械に挟まれる事故や、建設現場で大型機械に巻き込まれる事故が挙げられます。これらの事故は、単なる不注意や機械の不具合だけでなく、作業環境や安全教育の不足など複数の要因が絡んで発生します。
さらに、製造業における死亡災害の中で、最も多いのが挟まれ・巻き込まれ事故であり、全体の32.6%を占めています。また、死傷災害全体でも挟まれ・巻き込まれ事故が最多であり、その割合は18.0%に達しています。このデータから、製造業において挟まれ事故が重大なリスクであることが明白であり、特に注意が必要であることがわかります。
製造業における挟まれ事故・巻き込まれ事故
特に製造業においては、挟まれ、巻き込まれ災害の発生が多く、中央労働災害防止協会によると、2022年大業種分類で製造業が全体の約24%挟まれ巻き込まれ事故発生の割合を占めている状況です。
製造の作業現場では、ベルトコンベアやプレス機など可動部を持つ機械が多く、衣服や手が挟まれやすい環境であり、清掃・点検など運転中に行われる非定常作業も多いため、事故の危険が他の業種と比較しても高い傾向にあります。
対して、安全教育の頻度や作業前の確認手順、ルールは現場の指導者ごとに異なることも多く、作業者ごとに安全意識に差が出やすいのも現状です。
挟まれ事故や巻き込まれ事故は発生すると重大な被害を招くことが多く、その予防を講じることは急務です。したがって、管理側の企業や労働者はこれらの労働災害を未然に防止するために職場全体に徹底した安全対策と安全教育を実施することが求められています。
挟まれ事故と巻き込まれ事故の原因
企業が事故防止対策を講じる際、結果には必ず原因があるといった「因果律信条」(causality credo)に基づき、事故は特定の失敗や機能不全が原因であると考え、根本的な原因を見つけようとします。それ自体は間違ってはいませんが、事故の原因を機械の不具合や安全装置の未利用、作業中の不注意、マニュアルの徹底不足、そして労働者への安全教育不足といった特定の失敗や異常のような単一要因に求める傾向が強くなり、その失敗の背後にある多くの要因を見逃す確率が高くなります。それだけでは真の事故防止には繋がりません。
Safety-IIでは、物事がうまくいくプロセスと失敗するプロセスは本質的に同じであると考えます。なので、失敗の直接的な原因を調査のスタート地点と捉え、失敗へと突き進んだプロセスを理解しつつ、同時に日頃はどのようなプロセスで成功しているのかを調査します。日常業務の中で発生する変動、可変性に対しどのように調整をし、対処しているのか?そのプロセスをどのように支援・強化することが重要なのかを分析します。
本段落では、挟まれ・巻き込まれ事故の具体的な原因を紹介しつつ、それらを引き起こす背景要因を掘り下げ、どうすればベクトルをうまくいく方向に向けられるのか等、企業が根本的な対策を講じるための視点を提供します。
機械の不具合、安全装置の未利用
挟まれ事故や巻き込まれ事故の原因の一つとして、機械の不具合や安全装置の未利用が挙げられます。多くの機械には安全装置が付いていますが、その利用が徹底されていない場合や、機械自体に不具合がある場合、事故のリスクが高まります。例えば、古い機械や定期点検が行われていない機械は、故障や不具合が発生しやすく、それが原因で事故が発生することがあります。
作業中の不注意
作業中の不注意も大きな原因の一つです。労働者が疲労していたり、集中力が欠けていたりすると、機械の操作ミスや安全装置の未利用といった事態が発生しやすくなります。特に、長時間労働や過密なスケジュールが原因で、労働者が十分な休息を取れていない場合、事故のリスクはさらに高まります。
マニュアルの徹底(非定常作業)
非定常作業、つまり通常の作業手順とは異なる特殊な作業を行う際に、マニュアルが徹底されていないことも事故の原因となります。非定常作業では、通常の作業手順とは異なるリスクが伴うため、特別な注意が必要です。しかし、マニュアルが不十分であったり、従業員がその内容を理解していなかったりすると、事故のリスクが高まります。
労働者への安全教育不足
最後に、労働者への安全教育の不足も挟まれ事故や巻き込まれ事故の原因となります。新入社員や経験の浅い労働者は、機械の操作方法や安全装置の利用方法について十分な教育を受けていないことが多いです。その結果、誤った操作や安全装置の未利用が原因で事故が発生することがあります。企業としては、定期的な安全教育を実施し、全従業員が最新の安全情報を理解していることを確認する必要があります。
背景要因としてのシステム的問題
挟まれ事故や巻き込まれ事故の発生には、単なる不注意や機械の不具合といった直接的な原因だけでなく、その背後に潜むシステム的な問題が深く関わっています。例えば、作業者が過労や過密スケジュールにより十分な休息を取れていない場合、不注意や判断ミスが生じやすくなります。このような状況では、作業中のエラーは避けられない結果として発生し、システム全体の安全性を脅かす可能性が高まります。
また、安全装置の未利用が問題視される場合、その背景には、作業効率を優先する企業文化や適切な教育・訓練の不足があるかもしれません。実は、これらのシステム的背景要因は、なぜ失敗をしたのかといった視点だけで見つけることは困難です。このような擾乱の中でも“うまくいくように”調整をしている作業者が必ずいます。
そのような作業者に日頃はどのように工夫をして“うまくいくように”調整をして作業を遂行しているのか分析をすることでうまくいく時の基準が見えてきます。基準が明確になれば逸脱していることが分かりやすくなります。
事故を防ぐためには、システム全体の相互作用や人間の行動の可変性を理解し、プロアクティブな対策(先取りした対策)を講じる必要があります。上記のように、成功事例を分析し、その成功を支える要因を強化することでシステムの柔軟性と回復力を高めるための設計が可能になります。こうした包括的なアプローチにより、同様の事故の再発リスクを低減し、企業全体の安全性を向上させることが可能になります。
挟まれ・巻き込まれ事故の災害事例から学ぶ教訓
ここでは実際の事故事例を紹介し、それぞれの事故の原因から対策まで解説していきます。
横中ぐり盤(NCによる自動機)の暖機運転中、ドリルに巻き込まれた事故事例
– 概要
横中ぐり盤のドリルに作業者が巻き込まれ、身体が機械に巻き込まれた事故です。
– 原因
この災害の原因として、まず考えられるのは、暖機運転中にもかかわらず、運転中の機械に近づいてしまったことです。また、暖機運転中でありながら、機械加工が行われていない状況にもかかわらずドリルが装着されていたことも挙げられます。特に、ドリルの装着に関する判断が各機械オペレーターに委ねられていた点が問題となりました。
– 対策
まず、暖機運転を含め、機械運転中は作業者が誤って機械に近づかないようにすることが重要です。また、原則として暖機運転中にドリルを装着しないなどのルールを周知徹底することが重要です。さらに、ドリル装着の判断は機械オペレーター任せにせず、責任者が管理するなど作業者に対する安全教育を徹底し、基本的なルールを守ることが求められます。
ボール盤での穴あけ作業中の巻き込まれ事故
– 概要
ボール盤を使用し穴あけ作業をするため、ボール盤の台に部品を固定し、刃の交換作業を終えた直後、回転していたボール盤に上腕部が作業服ごと巻き込まれた事故事例です。
– 原因
まずボール盤のスイッチが停止位置に入れていなかったことが挙げられます。また、刃の取替え作業の際に、ボール盤の刃が回転していたことも事故の要因となりました。さらに、被災者の右上腕部が何らかの理由でボール盤の刃部と接触したことも原因の一つです。
– 対策
金属部品に穴を開ける準備の際には、ボール盤の主軸正逆転スイッチを必ず停止位置に設定することが重要です。また、刃の近くには非常停止機能を設置し、緊急時にすぐに機械を止められるようにするべきです。さらに、回転中の刃や回転部に手や身体を近づけないよう徹底します。労働者には、作業の危険性を理解させるためのリスクアセスメントを行い、安全作業手順書を作成・周知し、必要に応じて再教育を実施します。
ゴム成形用ロール機の清掃中に発生した巻き込まれ事故
– 概要
ロール機を清掃中、停止スイッチが押されたことを確認した後、ローラー上部のゴム寄せ部品に付着したゴムを取ろうとしましたが、ローラーが惰性で回転していたため、手が巻き込まれてしまった事故事例です。
– 原因
この災害の原因として、まず、対向するローラーの隙間に安全カバーや安全柵が設置されていなかったことが挙げられます。さらに、ローラーが完全に停止していない状態で手を入れてしまったこと、急停止装置を使用せず、通常の運転停止操作を行ったため、ローラーが惰性で回転していたことも原因です。加えて、十分な安全教育が行われていなかったことも一因です。
– 対策
対向するローラーの隙間に安全カバーや安全柵を設置し、作業者が危険にさらされないようにすることが重要です。また、危険箇所に手や身体の一部を入れる際には、機械が完全に停止していることを確認し、不意に作動しないようにすることが求められます。清掃や調整作業の際には、急停止機構を必ず作動させ、ローラーが直ちに停止するよう作業手順を変更することも必要です。非定常作業を含む作業標準を作成して、必ず守るべき事項を明文化し、労働者に周知徹底することが求められます。
テールゲートリフターの操作中に発生した挟まれ事故
– 概要
商品の積み下ろし作業にてテールゲートリフターの操作中、昇降盤の上でゲートを上昇させていた際、車両とゲートの間に足を挟みそうになってしまった事故事例です。
– 原因
こちらの災害の原因としては、作業者が昇降盤に乗った状態のまま、テールゲートリフターを操作していたことです。
– 対策
テールゲートリフター操作時は、作業者が昇降盤に乗った状態で昇降をしないことを徹底し、昇降時には、昇降盤のストッパーを使用し、積み荷を固定すべきです。テールゲートリフター作業者には、作業の危険性を理解させるための安全教育を事前に徹底することが求められます。
搬送用コンベアの清掃中に発生した巻き込まれ事故
– 概要
搬送用コンベアの清掃中に、ウェスがコンベアにひっかかり、指が巻き込まれ、切断されそうになってしまった事故事例です。
– 原因
こちらの災害の原因としては、清掃作業実施にあたり、コンベアを停止させることなく作業を実施していたことです。
– 対策
搬送用コンベアを始め、作業機械の清掃・包装紙等の除去、検査、修理等の作業等を行う際は、必ずまず機械の電源を切り、確実に停止したことを指差呼称で確認してから作業を実施すること。また、作業時守るべき事項を明文化し、作業者に事前に周知徹底することが求められます。
挟まれ事故と巻き込まれ事故の防止対策
定期的な機械の点検とメンテナンス
機械の点検とメンテナンスは、挟まれ・巻き込まれ事故を防ぐための基本的な対策です。機械が正常に動作しているかどうかを定期的に確認し、異常があればすぐに修理を行うことで、事故のリスクを大幅に減少させることができます。特に、安全装置が正常に機能しているかどうかを確認することが重要です。
作業環境・身だしなみの整備
挟まれ・巻き込まれ事故防止には、日頃から作業環境を整備しておくことも重要です。
具体的には、作業場内で5Sを徹底し、事故要因を常時排除することや、通路と作業設備の間を広めに確保することで、動線の交差を防ぎ、可動部への不用意な接近による事故を防ぐことなどがあげられます。
また、作業服は保護具を正しく着用することで衣服の巻き込みやヒューマンエラーを防ぐことにもつながります。これらの取り組みを現場全員で進めていくことが重要です。
作業手順の明確化とマニュアル強化
作業手順を明確にし、マニュアルを強化することで、作業者が安全に作業を行うためのガイドラインを提供することができます。特に、挟まれや巻き込まれのリスクが高い作業については、詳細な手順を示すことが重要です。それ以外にも、社内でスローガンや安全標語を作成することも効果的です。
従業員に日々意識してもらいやすくなり、業務中の不注意が軽減することが期待されます。
労働者への安全教育~動画活用のススメ~
労働者に対する安全教育は、挟まれ・巻き込まれ事故を防ぐための重要な対策です。
しかし、安全教育を実施したくても、社内に教育資料の用意がないことや、業務の兼ね合いでそもそも教育する時間を講師、従業員ともに設けられないことが多くあります。
また、安全教育を実施できたとしても、従業員に学ぶ意識がないことや、再教育の頻度が少ないことから知識が身につかないことも安全教育の課題です。
これらの課題において、動画やオンライン研修などの活用が注目されています。
動画やオンライン研修を活用すれば、これらの課題を解決し、効率的に学ぶことができます。
教育資料の準備や特別に実施する時間はもちろん不要となり、また、動画教材は情報がわかりやすく記憶に残りやすいこと、個人ペースで実施、再教育ができることも利点です。
例えば、ある企業ではオンラインコースを導入した結果、講師の招集コストを削減し、従業員の学習時間を柔軟に調整できるようになりました。その結果、従業員が自分の業務へ集中することができ、生産性が向上したという報告があります。
Safety-IIの考え方の導入
Safety-Ⅱとは、「何がうまくいったか(成功)」に焦点を当て、事故の未然防止に加えて、事故が起こらず、うまくいっている事例を活用して安全性を向上させるアプローチです。Safety-IIの考え方を導入することで、事故が起こらず日常的に成功を実現している状態を維持・強化し、全体としての安全性を向上させることができます。Safety-IIでは、なぜ事故が発生しないでいるかを分析し、その成功要因を増やすことに重点を置いています。これにより、挟まれ・巻き込まれ事故のリスクを低減し、事故の発生を防ぐことに寄与することが可能です。
まとめ
挟まれ事故や巻き込まれ事故は、労働現場での重大なリスクの一つであり、その発生原因は多岐にわたります。上述の通り、主な原因として機械の不具合や安全装置の未利用、作業中の不注意、マニュアルの不徹底、安全教育の不足などが挙げられます。
防止対策としては、定期的な機械の点検とメンテナンス、作業手順の明確化とマニュアルの強化、労働者への安全教育の徹底が重要です。また、Safety-IIの考え方を導入することで、日常的な成功要因を分析し、それを強化することで、全体的な安全性を高め、事故の発生を防ぐことが可能となります。
挟まれ・巻き込まれ事故を防ぐための安全教育につきましては、ラキールの「Lakeel OnlineMedia Service」を活用することをお勧めします。労働安全衛生などに関するアニメーションによる教育動画を700本以上提供しており、学ぶ意欲のない従業員でも興味が沸くよう工夫されているため、学びやすく理解しやすい内容となっています。挟まれ・巻き込まれ事故を防ぐための動画も多数用意しており、大変好評です。
サンプルムービー
についての動画も見てみる!
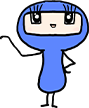
サンプル動画や、サービスの無料体験もできますので、ぜひ一度視聴してみてください。
LaKeel Online Media Serviceの動画を
無料でお試しいただけます。
\1分で完了!すぐ見れる/