職場の安全性を高めるためには、リスクを事前に把握し、適切な対策を講じることが重要です。そのための基本となる取り組みがリスクアセスメントです。
リスクアセスメントは、職場に潜む危険性や有害性を特定し、リスクを評価・低減する一連のプロセスを指します。これにより、労働災害の発生を未然に防ぎ、従業員が安心して働ける環境を整えることにつながります。今回は、リスクアセスメントの進め方や手法、リスクアセスメントシートの書き方などを詳しくご紹介します。職場の安全性を高めるための第一歩として、ぜひ参考にしてください。
リスクアセスメントとは
リスクアセスメントを正しく進めるには、まずリスクアセスメントで使われる言葉を把握することが必要です。
ここでは、リスクアセスメントとそれに関連する言葉を解説します。
リスクアセスメントの定義
リスクアセスメントとは、職場における潜在的な危険性や有害性を特定し、リスクを評価し、それを除去または低減するための一連の手法を指します。
事業者はリスクアセスメントの結果に基づいて適切な対策を講じる必要があり、事業者はリスクアセスメントの実施が努力義務とされています。
リスクと危険源の違い
「リスク」と「危険源」は、しばしば混同されがちな概念です。多くの人がこれらの用語を誤解したり、同じものだと捉えたりしてしまうことがありますが、実際にはそれぞれ異なる意味を持っています。リスクアセスメントを進めるにはリスクと危険源の違いを明確に区別して理解することが必要です。リスクとは、潜在的な危害が実際に発生する可能性の度合いと、発生した時の被害の程度を掛け合わせたものです。一方で、危険源とは、潜在的に危害の原因となり得るものを指します。
受け入れ可能なリスクと許容可能なリスク
リスクには「受け入れ可能なリスク」と「許容可能なリスク」、「許容不可能なリスク」といった3種類のリスクの考え方があります。職場のリスクを完全にゼロにすることは難しいですが、リスクの種類を理解することで、適切に対処することが可能です。
●受け入れ可能なリスク
受け入れ可能なリスクとは、危険源(hazard)によって労働者が負傷や疾病などのトラブルが発生しても、極めて軽微な影響にとどまり、大きな問題とならないリスクのことです。例えば、スポーツ選手が競技中に擦り傷を負った程度のリスクが当てはまります。
●許容可能なリスク
許容可能なリスクとは、受け入れ可能なリスクよりもトラブルの度合いが大きく、できれば避けたいリスクを指します。しかし、このようなリスクを回避するには、コストなどの面からみても現実的ではないため、許容可能なリスクとして対処することが多いです。例えば、スポーツ選手の捻挫や骨折は、受け入れ可能なリスクではないものの激しい競技の中では避けられない面もあるため、許容可能なリスクとなります。
●許容不可能なリスク
許容不可能なリスクとは、リスク低減のために必要な措置を講じた後でも残る、受け入れられないリスクを指します。このようなリスクは放置できず、直ちに改善や予防措置を取る必要があります。
安全とは
国際的には「安全」とは、2014年に「許容できないリスクがないこと」と定義されています。(ISO/IEC GUIDE 51:2014)つまり、リスクがゼロである必要はなく、“許容不可能なレベルのリスク”を取り除いた状態が安全だと見なされます。ゼロにできないリスクについては、リスクアセスメントを活用して“許容可能なレベル”まで低減することで、職場全体を安全な状態へと近づけることができると考えられています。
●Safety-Ⅱにおける安全とは
このように、従来の安全の考え方、いわゆる「Safety-Ⅰ」では、「失敗や事故が発生しない状態」を目指し、リスクや危険の除去を目指して、リスクアセスメントを行います。これはこれで非常に大切なアプローチですが、失敗を防ぐためのリアクティブ(反応的)な取り組みになる傾向があります。現代の複雑な社会システムにおいて完全に失敗を防ぐことは現実的ではなく、失敗による事故が発生してから対策を打つのでは不十分な安全管理となってしまいます。
これに対して、新しい安全の考え方である「Safety-Ⅱ」では、「すべてがうまくいくことを可能な限り多く実現する状態」を安全と再定義しています。この視点では、成功を促進するためのプロアクティブ(事前対策的)な取り組みが重視され、変化する状況に適応する能力や、日常的な調整や努力が安全の基盤となります。
例えば、大きな交差点で多くの人がぶつからずに横断歩道を渡る場面を想像してください。それぞれが動き、適応し、目的地へ向かうこの「何事もなくうまくいく日常」の背景には、多くの無意識の調整が存在しています。このような「動的な日常業務(Dynamic Non-Event)」が安全の本質なのです。
安全とは、単に「リスクをゼロにする」ことではなく、「許容できる範囲内でリスクを管理しつつ、システムがうまく機能する状態」を指します。この転換により、私たちは「失敗の防止」だけでなく、「成功を促進する」という新たな視点で、安全を捉え直すことが求められています。現代社会における安全を考える際には、従来のリスクアセスメントに加えて、この「動的で柔軟な安全」の視点で、日々の小さな努力や調整がどのようになされているのかを分析されることをお勧めします。
関連記事:ゼロ災とは?ゼロ災運動のメリットから取り組むべき労働安全衛生まで徹底解説!
リスクアセスメントの進め方
ここでは、リスクアセスメントの進め方を解説します。一般的に、以下の手順で進められます。
1.危険性又は有害性を特定する
機械・設備・原材料・作業行動・環境などにおける危険性や有害性を特定します。
危険性や有害性とは、従業員の死亡やケガや病気をもたらす物や状況のことです。例えば、安全対策が不十分な作業や有害な化学物質などが挙げられます。ヒューマンエラーや機械の故障なども念頭に置いて、作業全体の流れを確認して工程ごとの危険性や有害性を特定しましょう。従業員へヒアリングしたり、模擬作業を行って参加者同士で危険な点を指摘し合ったりすることも効果的です。また、リスクアセスメントを十分に実施することが難しい事業者は、厚生労働省の「作業別モデル対策シート」を利用しましょう。なお、職場に存在するさまざまな危険性や有害性を同時に調査することは難しいため、対象を絞って調査することが重要です。
2.リスクの見積もりと優先順位つけ
危険性や有害性を特定した後、それらが発生する確率、および従業員に与えるケガや病気の重篤度を見積もります。なお、リスクの評価基準は会社や評価者によって異なります。リスク評価の基準は会社や評価者によって異なるため、過去のリスクアセスメントの結果や労働災害の事例を基に基準を定めることが重要です。
重篤度の見積もりは低くなりがちですが、災害防止の観点からは、最悪の事態を想定して評価することが推奨されます。重篤度が高いと評価された場合には、その意見を尊重し、最も高いリスクを想定した評価が適切かどうかを再検討しましょう。また、担当者に加えて、実際の現場環境や作業に精通したスタッフを参加させ、さまざまな視点を取り入れることも不可欠です。
リスクを見積もった後は、見積もった点数に基づいて優先順位を設定しましょう。点数と優先順位の関係は、採用する見積もり手法によって異なります。以下は、加算式で点数を算出した場合の評価表(例)です。
リスクの評価表
点数 | 評価 | 優先度 | 対応措置 |
---|---|---|---|
20~12 | 直ちに解決すべき問題がある | IV | 直ちに中止または改善する |
11~9 | 重大な問題がある | III | 優先的に改善する |
8~6 | 多少問題がある | II | 計画的に改善する |
5以下 | 問題は少ない | I | 残っているリスクに応じて教育や人材配置をする |
3.リスク低減措置を検討・実施する
リスクを見積もった後は、リスク低減措置を検討・実施します。検討すべき措置にも優先順位があり、法令で定められた事項がある場合は必ず法を遵守しなければなりません。
リスクに対して行うべき安全衛生対策内容の優先順位は、以下のとおりです。
リスク低減措置の優先順位
優先順位 | 対策の種類 | 概要 | 具体的な対策例 |
---|---|---|---|
優先順位 1 | リスクの除去 | 設計や計画の段階における危険性又は有害性の除去又は低減 | ・危険な作業の廃止 ・作業内容の見直し ・危険な原材料や使用器具の変更 |
優先順位 2 | リスクの隔離 | 工学的対策 | ・ガード、インターロック、安全装置の設置など物的な対策 |
優先順位 3 | リスクの回避 | 管理的対策 | ・マニュアルの整備 ・立ち入り禁止措置 ・作業者への安全教育訓練など |
優先順位 4 | リスクの低減 | 個人用保護具の使用 | ・マスクや防護服の使用 ※1〜3の措置を講じても除去・低減しきれなかったリスクに対してのみ実施 |
実施すべき措置が決まったら、リスクアセスメントの担当者主導のもと、優先順位に従い措置を実施します。実施後も作業者に意見を求めつつ、作業性や生産性の影響を確認して、リスクの再見積もりを行いましょう。
また、リスク低減措置の実施により新たなリスクが発生する恐れもあるため、実施後も定期的に危険性や有害性を特定することが必要です。なお、リスク低減措置を実施しても、技術的・経済的な問題でこれ以上リスクを低減できず、大きなリスクが残ってしまう場合があります。その場合は、リスクアセスメントの実施記録にリスクが残っていることを記載して、作業者に内容を周知させて教育しましょう。
4.リスク低減措置導入による効果の記録と有効性を確認する
リスク低減措置を実施した後は、その効果と有効性を確認する必要があります。効果や有効性を確認することで、次回以降のリスクアセスメントや、安全衛生水準の向上に役立てられます。
また、導入による効果の記録は、危険性や有害性の特定からリスク低減措置の実施まで、全て記載して社内全体に共有することが重要です。社内で結果を共有すれば、リスクを周知させつつ従業員の安全意識を高められます。
なお、厚生労働省の「危険性又は有害性等の調査等に関する指針」で記録すべき内容として挙げられたのは、以下の項目です。
- 洗い出した作業
- 特定した危険性又は有害性
- 見積もったリスク
- 設定したリスク低減措置の優先度
- 実施したリスク低減措置の内容
出典:厚生労働省 > 「危険性又は有害性等の調査等に関する指針」
POINT 効率性と徹底性のバランスをとる
リスクアセスメントを進める際には、効率性と徹底性とのバランスを取ることが重要です。「失敗をゼロにする」ことを目指すSafety-Ⅰ的なアプローチでは、リスクを徹底的に洗い出し、可能な限り排除することが重視されます。しかし、その結果として現場の作業負担が増大し、生産性が低下する可能性があります。また、あまりに細部にわたる規定が現場の現実と乖離すると、安全行動そのものが疎かになるリスクも生じます。
現場の実態を踏まえ、適度に徹底しつつも実効性のある方法でリスクアセスメントを実施することで、職場全体の安全文化を強化し、より効果的なリスク低減につなげましょう。
注意:ただし、ほとんどの現場では効率を重視する傾向が強くあります。もし、安全を疎かにする傾向が強い組織風土をお持ちの場合は、Safety-Ⅰの可能な限り失敗を減らす施策をまずは実践してバランスをとってください。
リスクアセスメントの手法
リスクアセスメントにおいて、リスクの大きさを見積もる代表的な3つの手法を紹介します。算出された数値が高ければ高いほど、対策の優先順位が高いリスクといえます。
加算法
加算法とは、リスクの要素を分解して要素を段階分けして点数化し、それぞれの点数を足してリスク評価を行う手法です。
要素の例として、リスクの発生頻度や検知・回避の可能性や危害の重篤度などが挙げられます。
項目を増やしやすく点数が細かく出るため、合理的な優先順位が立てられます。
以下は、加算法で使うリスクの要素の点数表の例です。
危険源にさらされる頻度
リスクの発生頻度 | 点数 | 内容の目安 |
---|---|---|
頻繁 | 4 | 1日に1回程度かそれ以上 |
時々 | 2 | 週に1回程度 |
ほとんど無い | 1 | 半年に1回程度かそれ以下 |
リスクが発生したときに負傷又は疾病になる可能性の区分と評価の点数
可能性 | 点数 | 内容の目安 | |
---|---|---|---|
危険検知の可能性 | 危険回避の可能性 | ||
確実である | 6 | 事故が発生するまで 危険を検知する手段が無い |
危険に気が付いた時点では回避できない |
可能性が高い | 4 | 十分な注意を払わないと危険を検知できない | 専門的な訓練を受けていなければ 回避の可能性は低い |
可能性がある | 2 | 危険性・有害性に注目していれば 危険を検知できる |
回避手段を知っていれば 十分に危険が回避できる |
ほとんど無い | 1 | 容易に危険を検知できる | 気が付いた時点でケガをせずに危険を回避できる |
負傷又は疾病の重篤度(災害の程度)の評価基準
重篤度 | 点数 | 内容の目安 |
---|---|---|
致命傷 | 10 | 死亡や永久的労働不能につながるケガ・障害が残るケガ |
重症 | 6 | 1ヶ月以上休む必要があるケガ・一度に多数の被災者を伴う災害(休業災害) |
軽傷 | 3 | 1ヶ月未満で治るケガ・医師の措置を受ければ治るケガ(不休災害) |
軽微 | 1 | 手当を受ければ直ちに作業に戻れるケガ |
マトリクス法
マトリクス法とは、リスクの大きさを数値化せずに表を用いて見積もり、危険性の程度を判定する方法です。
リスクアセスメントでは、横軸に「重篤度」、縦軸に「リスクの発生頻度」を設定し、2つの軸を基にリスクのレベルを評価し、適切な対応策を決定します。この手法は、リスク低減措置の実施前と実施後の変化が分かりやすく、簡単にリスク評価ができるため、最も基本的で使いやすい手法とされています。
マトリクス法で使われる表の一例は次の通りです。
マトリクス法の表の一例
リスクの発生頻度 | 重篤度 | ||
---|---|---|---|
致命的・重大 | 中程度 | 軽度 | |
可能性が高い | 3 | 3 | 2 |
可能性がある | 3 | 2 | 1 |
ほとんど無い | 2 | 1 | 1 |
リスクグラフ法
リスクグラフ法とは、リスクの要素ごとに選択式で判別してリスク評価を行う手法です。一般的に、「危害の重篤度」「危険源にさらされる頻度」「回避の可能性」などに基づいて評価します。
以下はリスクグラフ法で使われる表の一例です。
リスクグラフ法の表の一例
危害の重篤度 | 危険源にさらされる頻度 | 回避の可能性 | リスク指数 | 優先度 |
---|---|---|---|---|
重度 | 日常的 | 困難 | 5 | 高 |
可能 | 4 | |||
まれ | 困難 | 3 | 中 | |
可能 | 2 | |||
軽度 | 日常的 | – | 2 | |
まれ | – | 1 | 低 |
リスクアセスメントシートの書き方
リスクアセスメントシートとは、リスクアセスメントの実施内容やリスクの見積もりなどを記録するシートのことです。
ここでは、厚生労働省「リスクアセスメント記録表」の項目をもとに、リスクアセスメントシートの書き方を紹介します。
参考:厚生労働省『リスクアセスメント記録表』
※リンクをクリックするとExcelファイルがダウンロードされます
1.基本項目
基本項目では、リスクアセスメント対象職場や実施管理者と、実施担当者の名前・実施日を記載します。リスクアセスメント対象職場に記載するのは、工場や事業所の名前です。実施担当者が複数人いる場合は、すべて記載しましょう。
2.作業名/工具、機械設備名
「フォークリフトによる運搬作業」や「鉄板加工作業」など、具体的な作業名を記載します。機械設備が対象となる場合は「天井クレーン1号機」というように、どの機械設備かわかるように記載しましょう。
3.危険性・有害性により発生のおそれのある災害
この項目では、作業環境における危険性や有害性によって発生する可能性のある災害を具体的に記載します。
災害発生のメカニズムを正確に把握し、防止策を適切に講じるため、「~なので、~する」「~なので、~になる」といった因果関係を明確に示す表現を用いることが重要です。
▼記載例
- 「高さ1.5mの場所で作業するので、バランスを崩すと転落する」
- 「切削作業中に切粉が飛散するので、目に入り網膜裂孔を引き起こす可能性がある」
- 「重量物を持ち上げる作業があるので、無理な体勢を取ると腰を痛める」
- 「可動部の近くで作業するので、誤って手を巻き込まれるおそれがある」
このように、具体的な作業状況とリスクを明確に記録することで、リスク低減措置の検討や効果的な安全対策の実施につなげることができます。
4.既存の災害防止対策/リスクの見積もり
目視確認や従業員への注意喚起など、現在行っている災害防止対策を記載します。また、重篤度・可能性・優先度の項目から、リスクの見積もりも記載します。すでに導入されている安全対策を明確にすることで、リスクを適切に評価し、追加の対策が必要かどうかを判断しやすくなります。
また、リスクの見積もりでは「重篤度」「発生可能性」「優先度」の観点から、リスクレベルを評価します。
5.リスク低減措置案/措置実施後の想定リスクの見積もり
この項目では、リスクを低減するための具体的な対策(リスク低減措置案)と、措置を講じた後のリスクレベルの見積もりを記載します。リスク低減措置を検討する際は、単に対策を考えるだけでなく、「その対策によってどの程度リスクが低減するのか」を明確にすることが重要です。
また、リスクの見積もりは、実施前と同じ評価基準で行うことで、リスク低減の効果を適切に比較・評価できます。
6.備考
備考欄には、残っているリスクへの対応を記載します。共有すべき事項がある場合は、必要に応じて記載しましょう。
まとめ
職場の安全を確保するために、リスクアセスメントは欠かせない取り組みです。技術の進化や作業環境の変化により、新たなリスクが生まれる中、適切な手法でリスクを特定・評価し、効果的な低減策を講じることが求められています。リスクアセスメントを進める際には、加算法やマトリクス法などを活用し、リスクの発生頻度や影響を正確に評価することが重要です。また、リスクアセスメントシートには低減措置案やリスクの見積もりを詳細に記録し、対策の有効性を明確にしましょう。リスクアセスメントを進める際には、「効率性」と「徹底性」とのバランスを取ることに注意が必要です。過度に細かいルールを徹底しようとすると、現場の負担が増し、生産性が下がることがあります。一方で、簡略化しすぎると安全対策が不十分になり、リスクを十分に低減できない恐れもあります。そのため、現場の実態を考慮し、現実的で実行可能な方法を取り入れることが大切です。
リスクアセスメントを効果的に行うには、職場の状況に合った現実的な方法で、従業員と協力しながら、実際に役立つ安全対策を進めていきましょう。その上で、対策がうまくいっているかを確認し、必要に応じて改善を重ねることで、安全への取り組みを職場全体に定着させていきましょう。
注意:ただし、ほとんどの現場では効率を重視する傾向が強くあります。もし、安全を疎かにする傾向が強い組織風土をお持ちの場合は、Safety-Ⅰの可能な限り失敗を減らす施策をまずは実践してバランスをとってください。
リスクアセスメントは一度行って終わりではなく、継続的な見直しと改善が必要です。適切な教育やツールを活用し、安全衛生教育を行う際は、LaKeel Online Media Serviceの活用がおすすめです。LaKeel Online Media Serviceには、安全衛生に関するアニメーション動画が700本以上用意されており、誰でも簡単に学べるのが魅力です。サンプル動画も用意しているので、ぜひ一度体験してみてください。
サンプルムービー
動画も見てみる!
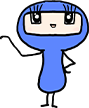
LaKeel Online Media Serviceの動画を
無料でお試しいただけます。
\1分で完了!すぐ見れる/