職場の安全と衛生を確保し、労働災害を未然に防止するために「リスクアセスメント」は欠かせません。しかし、リスクアセスメントについて明確に意味を説明することは難しいと感じている人も少なくないでしょう。リスクアセスメントとは、事業者及び労働者が、職場に潜在する危険性や有害性を認識し、リスクを低下させる対策を検討および実施、効果を確認するまでの手順のことです。この記事では、リスクアセスメントが重要な理由、そして実施することによる効果や手順を解説し、さらに事例も紹介します。
POINT
・リスクアセスメントとは、潜在的な危険や有害性を特定し、そのリスクを評価して適切な対策を講じること
・リスクアセスメントを行うことで、従業員が安全に働ける環境を用意する
・リスク低減措置を導入したら、必ず有効性を評価する
・リスクアセスメントを進める際には、効率性と徹底性とのバランスを取ることが重要
リスクアセスメントの定義
まずは、リスクアセスメントの定義と「リスク」「危険源」との違いを確認していきましょう。また「許容可能なリスクと受け入れ可能なリスク」そして「安全」についても解説します。
リスクアセスメントとは
リスクアセスメントとは、職場における潜在的な危険性や有害性を特定し、リスクを評価し、それを除去または低減するための一連の手法を指します。具体的には、危険性や有害性の調査、リスクの見積もり、優先度の設定、リスク低減措置の決定というプロセスを経て、適切な対策を講じることが求められます。リスクアセスメントは、職場の安全衛生意識を高め、危険な工程を速やかに改善し、労災を未然に防ぐための重要な手順です。
労働安全衛生法第28条の2では、「危険性又は有害性等の調査及びその結果に基づく措置」として、製造業や建設業などの事業者に対してリスクアセスメントの実施が努力義務とされており、厚生労働省からは「危険性又は有害性等の調査等に関する指針」が公表され、その適切な実施を促進しています。
リスクと危険源の違いとは
「リスク」と「危険源」は、しばしば混同されがちな概念です。多くの人がこれらの用語を誤解したり、同じものだと捉えたりしてしまうことがありますが、実際にはそれぞれ異なる意味を持っています。リスクとは、潜在的な危害が実際に発生する可能性の度合いと、発生した時の被害の程度を掛け合わせたものです。一方で、危険源とは、潜在的に危害の原因となり得るものを指します。労働安全衛生法では、こちらも「危険性又は有害性」と表現されています。具体的には、危険源が存在していても、事故が起こる可能性が低い場合はリスクが低いといえます。しかし、発生の確率が低くても、万が一事故が発生した場合の影響が甚大であれば、リスクは高いと評価されます。なお、ISO12100(JIS B9700)における用語定義は以下の通りです。
・「リスク(risk)」
危害の発生確率と危害のひどさとの組合せ。
・「危険源(hazard)」
危害を引き起こす潜在的根源。
許容可能なリスクと受け入れ可能なリスク、許容不可能なリスクとは
リスクには「受け入れ可能なリスク」と「許容可能なリスク」、「許容不可能なリスク」といった3種類のリスクの考え方があります。職場のリスクを完全にゼロにすることは難しいですが、リスクの種類を理解することで、適切に対処することが可能です。
・受け入れ可能なリスク
受け入れ可能なリスクとは、危険源(hazard)によって労働者が負傷や疾病などのトラブルが発生しても、極めて軽微な影響にとどまり、大きな問題とならないリスクのことです。例えば、スポーツ選手が競技中に擦り傷を負った程度のリスクが当てはまります。
・許容可能なリスク
許容可能なリスクとは、受け入れ可能なリスクよりもトラブルの度合いが大きく、できれば避けたいリスクを指します。しかし、このようなリスクを回避するには、コストなどの面からみても現実的ではないため、許容可能なリスクとして対処することが多いです。例えば、スポーツ選手の捻挫や骨折は、受け入れ可能なリスクではないものの激しい競技の中では避けられない面もあるため、許容可能なリスクとなります。
・許容不可能なリスク
許容不可能なリスクとは、リスク低減のために必要な措置を講じた後でも残る、受け入れられないリスクを指します。このようなリスクは放置できず、直ちに改善や予防措置を取る必要があります。
安全とは
国際的には「安全」とは、2014年に「許容できないリスクがないこと」と定義されています。(ISO/IEC GUIDE 51:2014)つまり、リスクがゼロである必要はなく、“許容不可能なレベルのリスク”を取り除いた状態が安全だと見なされます。ゼロにできないリスクについては、リスクアセスメントを活用して“許容可能なレベル”まで低減することで、職場全体を安全な状態へと近づけることができると考えられています。
●Safety-Ⅱにおける安全とは
このように、従来の安全の考え方、いわゆる「Safety-I」では、「失敗や事故が発生しない状態」を目指し、リスクや危険の除去を目指して、リスクアセスメントを行います。これはこれで非常に大切なアプローチですが、失敗を防ぐためのリアクティブ(反応的)な取り組みになる傾向があります。現代の複雑な社会システムにおいて完全に失敗を防ぐことは現実的ではなく、失敗による事故が発生してから対策を打つのでは不十分な安全管理となってしまいます。
これに対して、新しい安全の考え方である「Safety-Ⅱ」では、「すべてがうまくいくことを可能な限り多く実現する状態」を安全と再定義しています。この視点では、成功を促進するためのプロアクティブ(事前対策的)な取り組みが重視され、変化する状況に適応する能力や、日常的な調整や努力が安全の基盤となります。
例えば、大きな交差点で多くの人がぶつからずに横断歩道を渡る場面を想像してください。それぞれが動き、適応し、目的地へ向かうこの「何事もなくうまくいく日常」の背景には、多くの無意識の調整が存在しています。このような「動的な日常業務(Dynamic Non-Event)」が安全の本質なのです。
安全とは、単に「リスクをゼロにする」ことではなく、「許容できる範囲内でリスクを管理しつつ、システムがうまく機能する状態」を指します。この転換により、私たちは「失敗の防止」だけでなく、「成功を促進する」という新たな視点で、安全を捉え直すことが求められています。
現代社会における安全を考える際には、従来のリスクアセスメントに加えて、この「動的で柔軟な安全」の視点で、日々の小さな努力や調整がどのようになされているのかを分析されることをお勧めします。
リスクアセスメントが重要な理由
ここでは、リスクアセスメントが重要な理由を解説するとともに、目的や歴史を振り返っていきます。また、「立場別」からみたリスクアセスメントの必要性についても解説します。
リスクアセスメントの目的
リスクアセスメントの目的は、職場環境や業務内容に潜むリスクを特定し、それを評価して、労働者が安全に働ける環境を整えることにあります。これまで、職場でのケガや事故を防止するための安全対策としては、発生した事故の原因を調査し、再発防止を各職場に徹底させるという手法が一般的でした。この手法の場合、顕在化したリスクへの安全対策は取れましたが、潜在化している危険性や有害性には対応できません。そこで、自主的に職場の潜在化している危険性や有害性を見つけ出し、事故を未然に防ぐために確立されたのがリスクアセスメントです。
リスクアセスメントの歴史~ローベンス報告の役割~
ローベンス報告とは、1972年にイギリスで報告された、労働安全衛生に関する報告書です。この報告は、当時の労働安全法規の問題点に焦点を当てたもので特に以下の3つの課題を指摘しました。
1つ目は、「法律が多すぎて煩雑」であり、すでに9つの法令群と約500もの細かな規則が存在し、それに対処するだけで手一杯になっていたこと。2つ目は、「法律の多くが本質的に不備である」ため、現場の管理者が理解しにくく、効果的に運用されていなかったこと。そして3つ目は、「行政の管轄が細分化されて非効率」になっており、効率的な安全衛生管理が行われていなかった点です。
ローベンス報告を受けて、1974年に4章84条で構成された労働健康安全法(Health and Safety at Work etc. Act 1974。略称「HSWA」)が制定されました。
HSWAは「自主的かつ包括的な安全衛生管理」の枠組みを打ち立て、その後に制定された「Management of Health and Safety at Work Regulations(1992年)」などの規則によって “リスクアセスメント”の実施が企業に義務づけられるようになりました。こうした取り組みによってイギリスは労災死亡率が低い国として知られるようになり、日本でもこの流れを参考にして 2006年にリスクアセスメントの実施が努力義務化されています。
リスクアセスメントが必要な理由
リスクアセスメントは、職場の安全と衛生を確保し、労働災害を未然に防ぐために欠かせない取り組みです。その本質は、潜在的な危険や不確実性を「未知のまま」にせず、「既知」に変えることにあります。職場で起こり得るリスクを特定し、その影響や発生の可能性を適切な対策を講じることができます。人間が安全に生活するために重要な要素として、『未来を予測できること』が挙げられます。未来を予測することで、未知の状況に適切に対応し、必要な対策を講じることが可能になるため、その観点からもリスクアセスメントは重要と言えるでしょう。
リスクアセスメントは、この「未知を既知に変える」ため、職場の安全確保に大きく寄与します。なお、従業員・経営層・下請け先など立場によってリスクアセスメントに求められる内容や目的は異なります。それぞれの視点からリスクアセスメントの必要性を確認してみましょう。
・「従業員」
リスクアセスメントは、職場における潜在的な危険を特定し、そのリスクを最小限に抑えるための重要なプロセスです。従業員が日常業務を安全に行えるよう、物理的・精神的なリスクを事前に評価することで、怪我や病気の発生を防止することに役立ちます。また、作業プロセスや設備、職場環境の中にある問題点を発見し、改善するための具体的な対策を立てることができます。これにより、従業員の健康やストレスを軽減し、より快適で効率的な労働環境を提供することが可能です。
従業員が安全に働ける職場環境が整っていると、仕事に対する安心感が生まれ、モチベーションも向上します。リスクが低い職場環境は、従業員が効率的に作業を進められるため、生産性向上にも寄与します。人手不足が深刻化するこの時代に、従業員の離職を防ぎ、安心して長期就労できる職場を整えるためにも、リスクアセスメントの推進は必要です。
・「経営層」
経営層にとってリスクアセスメントは、企業全体のリスク管理戦略と法的リスク回避に不可欠です。従業員の安全、法令遵守、環境負荷などのリスクを適切に評価することで、事故やトラブルを未然に防ぎ、法的リスクの回避にもつながります。
・「下請け先」
下請け先に業務を委託している場合、リスクアセスメントの結果を共有して、下請け先の労災を防止する取り組みが必要です。安全衛生上注意すべき点や、製造などで取り扱う原材料の危険性・有害性、そして応急処置などについて情報を提供し、下請け先の職場や従業員の安全を確保します。
リスクアセスメントの最終責任は事業者(経営層)にありますが、従業員や下請け先も情報共有や危険源の指摘などを通じて協力することが不可欠です。
リスクアセスメントで得られる効果
ここでは、リスクアセスメントを実施することで得られる5つの効果を解説します。
リスクの明確化と認識の共有ができる
職場内に潜む「危険性」や「有害性」を洗い出すことで、事業所や会社全体のリスクが明確化できるだけでなく、認識の共有ができます。職場の身近に潜むリスクを把握できれば、業務経験や熟練度に関係なく、全従業員が安全意識を高められるでしょう。
優先順位を明確化できる
職場内に存在するさまざまなリスクの優先順位を明確化できます。優先順位の高いリスクから低減を図ることで、少ない労力やコストで最大限の効果を得られるのです。
残ったリスクに対して「守るべき決めごと」の理由が明らかになる
すべてのリスクをゼロにすることは難しいため、残るリスクもあります。これらに対しては、「守るべき決めごと」やルールが設定されますが、リスクアセスメントを行うことでなぜそのルールが必要なのか、その理由が従業員全体に明確になります。
職場全員で行うことで、「危険」に対する意識が高まる
リスクアセスメントは本来、潜在的な危険を客観的に評価し、具体的な対策を講じることが主な目的です。しかし、これを職場全員で共有し、協力しながら実施する過程で、自然と「危険」に対する意識も高まるという副次的な効果が得られます。全員が危険源を身近に感じ、声を掛け合うことで安全への責任感が高まり、結果として職場全体に“安全文化”が浸透します。
職場全体の安全性が高まり、事故の防止につながる
リスクアセスメントでは、職場内に潜むリスクを特定し、それらに対する適切な対応策を検討・実施します。この過程を通じて、日常業務が円滑に進む仕組みが強化され、予期せぬ事態にも適切に対応できる職場環境が整います。その結果、事故や労災の発生リスクが低減し、職場全体の安全性が向上します。
リスクアセスメントの手順
リスクアセスメントは、厚生労働省が発表している「危険性又は有害性等の調査等に関する指針」を参考にしながら、基本的な手順を基に実施することが求められます。ここでは、以下の通りリスクアセスメントの具体的な手順を紹介します。
1.危険性又は有害性を特定する
まず、機械や設備、原材料、作業行動や環境などを調査し危険性や有害性を特定します。また、作業を実施するにあたっては、現場実態を踏まえ、定常的な作業のみならず、非定常作業も含んだ以下のような情報や資料を事前に入手しておきましょう。
- 作業標準、作業手順書等
- 仕様書、化学物質等安全データシート(MSDS)等、使用する機械設備 、材料等に係る危険性又は有害性に関する情報
- 機械設備等のレイアウト等、作業の周辺の環境に関する情報
- 作業環境測定結果等
- 混在作業による危険性等、複数の事業者が同一の場所で作業を実施する状況に関する情報
- 災害事例、災害統計等
- その他、調査等の実施に当たり参考となる資料等
引用:厚生労働省 > 「危険性又は有害性等の調査等に関する指針」
2.リスクの見積もりと優先順位つけ
リスクを見積もる方法として、ここでは3つ紹介します。
・数値化による加算方法
負傷または疾病の発生度合いと重篤度を一定の基準で数値化し、それらを加算してリスクを見積もる方法です。
・マトリクス法
負傷または疾病の発生度合いとその重篤度を区分し、表の縦軸と横軸にあてはめてリスクを見積もります。
・枝分かれ図を用いた方法
負傷または疾病の発生度合とその重篤度を段階的に分岐させて、リスクを見積る方法です。
引用:厚生労働省 > 「職場のリスクアセスメント」
厚生労働省 > 働災害を防止するため リスクアセスメントを実施しましょう
リスクを見積もったら、次は優先順位を決めましょう。見積もった数値が高いほど優先度も高くなります。また、リスクを見積もるにあたり、評価者によって結果にバラつきが出ないように、以下のような対策をとることが重要です。
- 評価に偏りが生じないよう、性別や年齢にとらわれず、複数の評価者による共同評価を行う
- 評価者が主観に左右されないよう、評価基準を具体的かつ明確に定める
- 職場環境や実情に即した評価基準を策定する
- 評価者に対しては、評価の手法や基準に関するトレーニングを提供し、理解を深める
3.リスク低減措置を検討・実施する
リスクを見積もって優先順位をつけたら、リスク低減措置を検討・実施します。リスク低減措置は、法令に定められた事項がある場合にはそれを必ず遂行するとともに、次に掲げる優先順位で検討し実行することが重要です。
- 設計や計画の段階における危険性又は有害性の除去又は低減
危険な作業の廃止・変更、危険性や有害性の低い材料への代替、より安全な施工方法への変更等 - 工学的対策
局所排気装置、防音囲いの設置等 - 管理的対策
マニュアルの整備、立ち入り禁止措置、ばく露管理、教育訓練等 - 個人用保護具の使用
上記1~3の措置を講じた場合においても、除去・低減しきれなかったリスクに対して実施するものに限られます
引用:中央労働災害防止協会 > リスクアセスメントの進め方と効果、3 リスクの低減措置の優先順位
4.リスク低減措置導入による効果の記録と有効性を確認する
リスクアセスメントは、リスク低減措置を実施して終了するものではありません。その結果を記録し、低減措置が効果的であったかを評価することが重要です。効果が確認された低減措置は他のエリアやプロセスにも展開できますが、効果が不十分であった場合は、その対策を見直し改善する必要があります。なお、厚生労働省が公表している「危険性又は有害性等の調査等に関する指針」では、記録すべき内容を以下のように定めています。
事業者は、次に掲げる事項を記録するものとする。
(1)洗い出した作業
(2)特定した危険性又は有害性
(3)見積もったリスク
(4)設定したリスク低減措置の優先度
(5)実施したリスク低減措置の内容
引用:厚生労働省 > 「危険性又は有害性等の調査等に関する指針」
POINT 効率性と徹底性のバランスをとる
リスクアセスメントを進める際には、効率性と徹底性とのバランスを取ることが重要です。「失敗をゼロにする」ことを目指すSafety-I的なアプローチでは、リスクを徹底的に洗い出し、可能な限り排除することが重視されます。しかし、その結果として現場の作業負担が増大し、生産性が低下する可能性があります。また、あまりに細部にわたる規定が現場の現実と乖離すると、安全行動そのものが疎かになるリスクも生じます。
現場の実態を踏まえ、適度に徹底しつつも実効性のある方法でリスクアセスメントを実施することで、職場全体の安全文化を強化し、より効果的なリスク低減につなげましょう。
注意:ただし、ほとんどの現場では効率を重視する傾向が強くあります。もし、安全を疎かにする傾向が強い組織風土をお持ちの場合は、Safety-Ⅰの可能な限り失敗を減らす施策をまずは実践してバランスをとってください。
リスクアセスメントの事例
ここでは、「食品製造業」「製造業」「建設業」における、リスクアセスメントの事例を紹介します。
食品製造業
食品製造業では、機械や刃物を使用する工程が多く、切傷や機械による巻き込まれ、転倒といった労働災害のリスクがあります。こうしたリスクを減らすため、食品製造業では保護手袋の使用や機械の安全教育、現場での注意喚起などが重要です。これらの対策を効果的に実施するために、リスクアセスメントが導入され、作業環境の安全性が高められています。
<食品製造業A社におけるリスクアセスメント事例>
食品製造業のA社では、防火管理委員会および安全衛生委員会が主導し、各部署の委員がリスクアセスメントを実施しました。リスクが抽出された後、工場長や製造管理責任者の承認を経て、対策が講じられ、作業員に周知されています。A社でのリスクアセスメントは、以下の手順で行われています。
- 委員会からリスクアセスメントの実施が各部署にアナウンスされる。
- 各部署がリスクを抽出し、対策案を評価・検討した後、工場長や製造管理責任者に承認を依頼。
- 承認後、委員会で対策案が説明され、現場作業員に周知し、対策を実施。
A社では、設備の改善工事前や稼働前にリスクアセスメントを実施し、事故リスクを低減。また、業界や近隣企業で事故が発生した際には、類似リスクを速やかに評価し、追加のリスクアセスメントを実施しています。
製造業
製造業では多くの機械設備を使った作業が多岐にわたるほか、危険物の取り扱いも頻繁に行われるため、労働災害が発生しやすく、その結果が深刻なものとなるリスクも高いという特徴があります。製造業でよく見られるリスクとしては、高所からの転落や転倒、機械への挟まれや巻き込まれなどがあり、多様な危険が存在します。また、製造業全体で似た作業が多いため、リスクアセスメントの事例も数多く蓄積されています。
リスクアセスメントは、新しい設備の導入や工事、作業内容の導入・変更時だけでなく、日常業務においても徹底して行われています。この実施においては、固定観念にとらわれず、関係者を幅広く集めてリスクを抽出することが重要です。さらに、実施結果の共有や危険箇所の明示を通じて、従業員のみならず職場に立ち入る外部者への注意喚起も行われています。
<製造業B社におけるリスクアセスメント事例>
B社では、作業、設備、変更管理の3つの場面でリスクアセスメントを実施しており、それぞれ異なる手法と実施者が担当しています。
1. 作業リスクアセスメント
対象: 工事や作業内容
実施手順: 危険源の抽出 → 評価 → 対策立案 → 実施
実施者: 実際の工事等を担当する外注先の社員が実施し、所管部署がモニタリングを行います。
2. 設備リスクアセスメント
対象: 設備の導入・維持管理
実施手順: 危険源の抽出 → 評価 → 対策立案 → 確認 → 実施
実施者: 運転課を中心としたチームが担当し、課長や所長が確認・承認します。
3. 変更管理時リスクアセスメント
対象: 設備やプロセス変更時
実施手順: 変更点確認 → 危険源の抽出 → 評価 → 対策立案 → 審議 → 実施前の確認 → フォローアップ
実施者: 管轄部署が行い、安全審査会議で最終審議が行われます。
実施頻度と手法
リスクアセスメントの実施頻度は、定期的な実施と不定期な実施に分かれています。定期的な実施では、既存設備に対し、5年で一巡するよう計画的にリスクアセスメントを実施しています。一方、不定期な実施では、作業の発生時や設備の新設・増設時、またプロセスや製品品質の変更管理が行われる際に、状況に応じて随時リスクアセスメントを行います。手法としては、作業は独自の危険予知(RKY)方式、設備はHAZOP、変更管理時は安全性評価チェックシートを使用して実施。
建設業
建設業では、高所作業や重量物の運搬、大型重機やさまざまな工具の使用が伴うため、転落、転倒、衝突、工具による怪我など、多様なリスクが発生します。また、工事のスケジュールが厳しく設定されることも多く、作業員の休息が十分に取れない状況が生じやすいという課題も抱えています。さらに、建設現場では元請業者と下請業者が共同で作業することが多く、同時進行の作業によるリスクも考慮する必要があります。
ある建設プロジェクトでは、リスクアセスメントの担当者が工事の計画段階からスケジュールに基づいて作業をすべて網羅し、作業者に対するリスクの周知と安全教育を徹底しました。この取り組みにより、現場での安全対策が強化され、リスクを効果的に低減することができました。
まとめ
リスクアセスメントは、職場の安全と衛生を確保し、労働災害や事故を未然に防ぐために欠かせない取り組みです。その本質は、潜在的な危険やリスクを「未知」の状態から「既知」に変え、それに基づく適切な対策を講じることで、職場全体の安全性を向上させることにあります。ただし、リスクアセスメントを進める際には、「効率性」と「徹底性」とのバランスを取ることに注意が必要です。
過度に細かいルールを徹底しようとすると、現場の負担が増し、生産性が下がることがあります。一方で、簡略化しすぎると安全対策が不十分になり、リスクを十分に低減できない恐れもあります。そのため、現場の実態を考慮し、現実的で実行可能な方法を取り入れることが大切です。
リスクアセスメントを効果的に行うには、職場の状況に合った現実的な方法で、従業員と協力しながら、実際に役立つ安全対策を進めていきましょう。その上で、対策がうまくいっているかを確認し、必要に応じて改善を重ねることで、安全への取り組みを職場全体に定着させていきましょう。注意:ただし、ほとんどの現場では効率を重視する傾向が強くあります。もし、安全を疎かにする傾向が強い組織風土をお持ちの場合は、Safety-Ⅰの可能な限り失敗を減らす施策をまずは実践してバランスをとってください。
企業はリスクアセスメントを適切かつ確実に実践して、従業員が安心して働ける環境を整備する責任があります。
まずその第一歩として、従業員への安全衛生教育を行うことが重要です。
安全衛生教育を行う際は、LaKeel Online Media Serviceの活用がおすすめです。LaKeel Online Media Serviceには、安全衛生に関するアニメーション動画が700本以上用意されており、誰でも簡単に学べるのが魅力です。サンプル動画も用意しているので、ぜひ一度体験してみてください。
サンプルムービー
動画も見てみる!
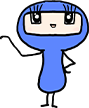
LaKeel Online Media Serviceの動画を
無料でお試しいただけます。
\1分で完了!すぐ見れる/